Phoenix Performs Successful Ballast Tank Repair
Phoenix International is an employee-owned, ISO 9001-2015 Management System certified marine services contractor providing manned and unmanned underwater solutions, design engineering, and project management services to a diverse set of clients worldwide.
Through their Underwater Ship Repair & Maintenance Division, they have been performing quality inspection, repair, and maintenance (“IRM”) operations on commercial ships, oil and gas platforms, and marine infrastructure for over 20 years. Whether it is a planned inspection – or an emergency repair, their teams of highly qualified and experienced personnel provide services 24/7 to aid clients in avoiding critical downtime.
Phoenix is approved by all appropriate classing agencies and is well-versed in planning, coordinating, and successfully carrying out waterborne IRM worldwide. All work is performed in adherence to strict Phoenix safety protocols, resulting in safe and timely underwater services documented with professional and concise reports.
Project Kick-Off
In the second quarter of 2024, a Phoenix dive team was tasked with the repair of damage found by a third-party diver in a ballast tank of a capital floating asset of an international offshore energy services company. The client applied a large internal concrete patch to the damaged area to slow the ingress of water into the tank while Phoenix divers and equipment mobilized. Due to limited visibility at its location in Port Fourchon, the vessel was moved to Block 83 of the U.S. Gulf of Mexico for repairs.
Figure 1. Damage with relief cuts.
A thorough bottom survey by Phoenix divers revealed that the damage extended past the area initially specified and an external cofferdam measuring 11 ft forward-aft and 7 ft port-starboard was designed, constructed on-site, and installed by Phoenix, thereby eliminating all water ingress. Then, inside the damaged ballast tank, Phoenix divers removed the concrete patch and washed and flushed the area to allow further internal inspection.
With a proper inspection completed and witnessed by an American Bureau of Shipping (“ABS”) surveyor, a repair plan was agreed to by the client, Phoenix, and ABS. Due to the large extent of the damage, which was in the way of multiple transverse frames, an internal box patch was specified via a hull insert.
Project Specifications and Completion
The temporary repair specified was a fully welded, half-inch thick internal steel box. Prior to installation of the box, all fracture terminations were first cut with a four-inch diameter hole to arrest any potential fracture propagation. Once the fracture stops had been cut, all limber holes were covered with a half-inch plate and fully seal welded. These tasks were conducted using several of Phoenix’s 53 certified welding procedure specifications . These specifications, approved by various government and classing societies, greatly reducing client cost by virtue of their pre-qualification.
Figure 2. Post Internal cofferdam built.
The second phase of the project consisted of building and fully seal-welding the box and the welding stiffeners to the top of the box to ensure requisite strength and structural integrity. A smaller internal box was also fabricated and installed over the damaged area forward of one transverse frame. The external cofferdam was then flooded, and the internal boxes checked for leaks. One additional damaged and leaking area was discovered in the weld seam on the port side of the second major longitudinal from centerline. The external cofferdam was again pumped dry, the leak repaired via welding, and marine epoxy was applied over the weld repair.
Figure 3. Post internal cofferdam built.
The cofferdam was once again flooded, and all repairs were satisfactorily leak tested. Commenting on the project, Errol Gritten, technical operations manager and certified welding inspector, stated, “We are pleased that our client trusted us with this repair, and I am incredibly proud of our team for safely performing the works with minimum downtime to the vessel and allowing it to get back to work.”
About the Author
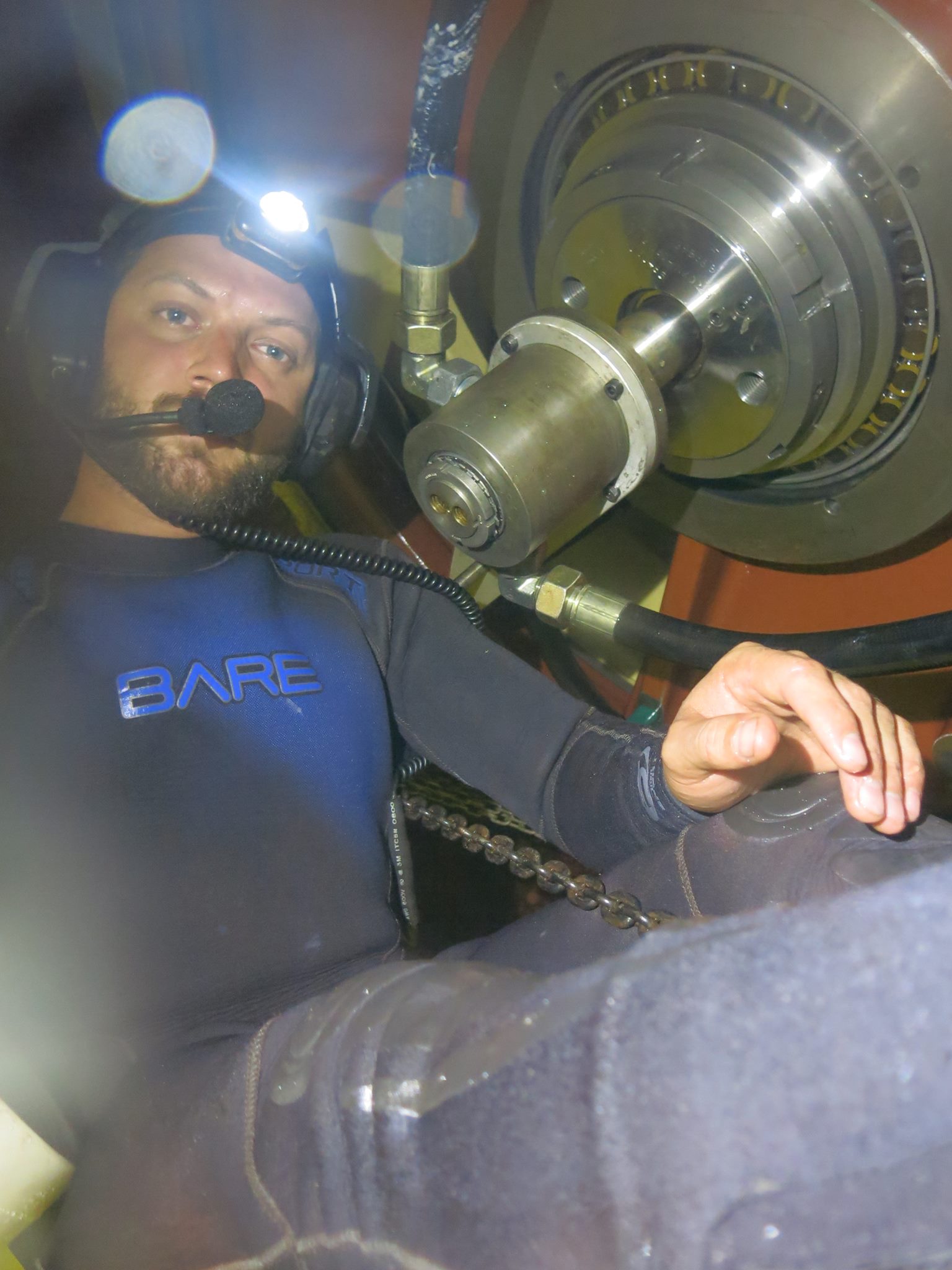
Errol Gritten
Phoenix International Holdings, Inc.
egritten@phnx-international.com